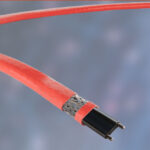
Winter Preparation; Electrical Heat Trace
September 20, 2022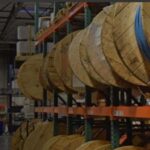
Cable Types Explained
January 30, 2023Motor Starters, Soft Starts and VFD’s
Electric motors are everywhere; office buildings, water treatment plants, hospitals, hockey arenas, parks, and so on. This is especially true in industrial settings. Industrial facilities utilize electric motors to run a wide variety of processes including pumps, fans, conveyors, belts and augers.
Over the years, engineers have developed various methods for controlling these motors. There are key differences between each method and some important factors to consider when choosing the best option for your application.
Motor Starter
The most cost-effective and prevalent device for controlling an electric motor is the motor starter. Motor starters are simple devices. They have a set of electrical contacts that are springloaded to disconnect the power unless they’re held together by an electromagnetic coil.
Starters also have a set of “overloads” that will break the connection if they get too warm. This is how starters protect themselves from overcurrent.
Starters are effective and reliable. However, they are basically glorified light switches. When controlled by a starter, motors are either on or off and there is no middle ground.
As a result, there is no way to control the speed of the operation you’re running. Another drawback is excessive wear and tear on the equipment due to the immediate torque applied when the starter is engaged.
When the coil pulls the contacts together on a starter, the connection is instant. The motor is flooded with electrical current as it goes from stationary to running. This is known as “inrush current” and it is much higher than the normal operating current for the motor. This puts tremendous stress and torque on the motor, the shaft, and all the moving equipment. The starter doesn’t allow the motor to ‘ramp up’ gently.
In simple terms, motor starters are hard on things. Maintenance costs are higher as the equipment is exposed to higher stress levels that create mechanical issues. The high inrush current and inability to control the motor speed increases energy bills and inflates operating costs.
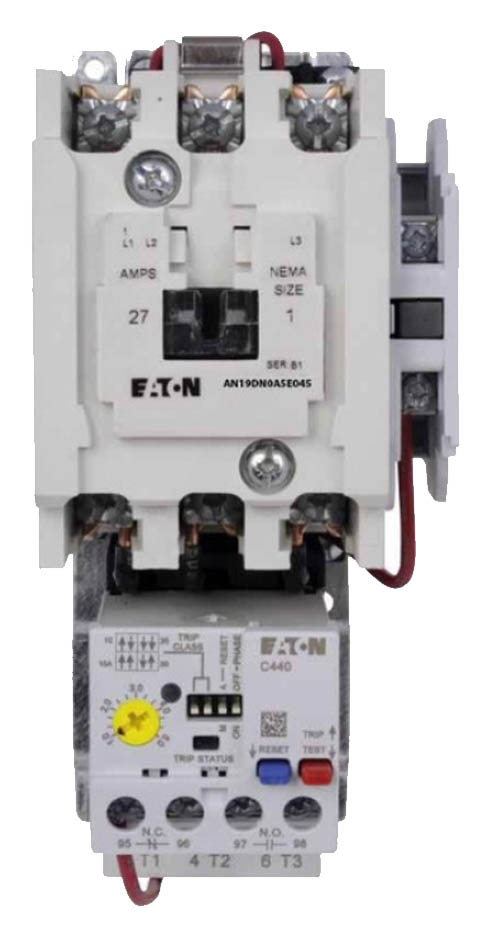
In applications where the motor is up against high inertia (water pumps), the in-rush current becomes a bigger problem. This leads us to the next device, the Soft Start.
Soft Start
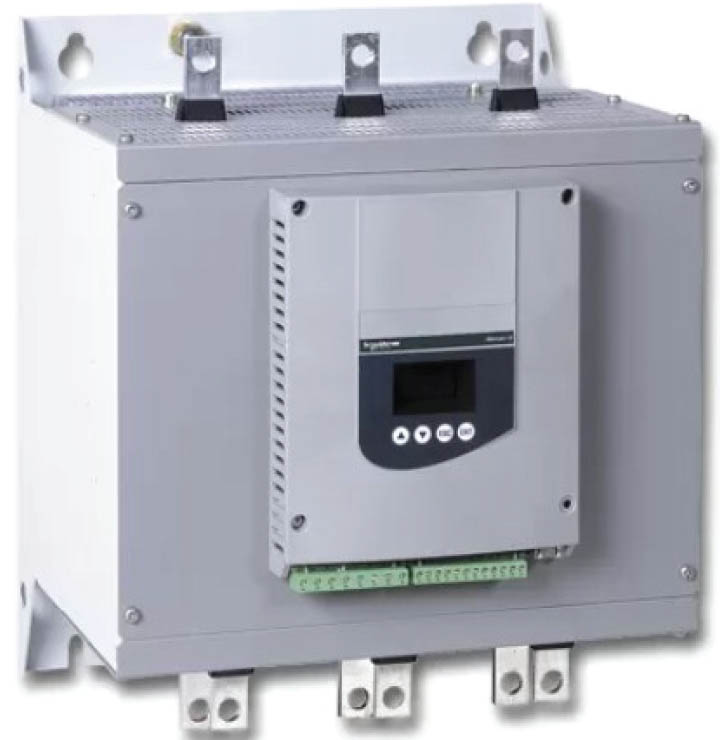
A Soft Start is a device that operates similarly to a motor starter but limits the inrush current to help ease the motor into full operation. It does this by using thyristors or a pattern of solid-state switches which allow the voltage to increase at a slower rate
The motor, therefore, starts more gradually and avoids the large torque applied if using a common starter.
Soft starts are significantly more expensive than motor starters and take up a larger physical footprint. Another drawback is that they don’t offer speed control.
Once the motor slowly ramps up to full speed, that’s where it stays until you shut the motor down. If your process requires speed control, you must move to a Variable Frequency Drive.
VFD
Variable Frequency Drives, commonly known as VFD’s, offer full speed control, slow start capabilities, and energy savings. VFD’s work by breaking down the incoming voltage and changing the frequency of the current.
In a typical setup, VFD’s take incoming AC power and channels it through a series of diodes. Diodes are electrical devices that allow the flow of electricity in only one direction (similar to a check valve in a water line).
The current flows out of the diodes, now in one direction, as DC power. The DC power is smoothed out by a capacitor and then enters into an IGBT inverter.
These special inverters use highspeed switches to alternate the actual route of the power, essentially recreating the output current as AC power. The IGBT Inverter also staggers the switching which, when done at select intervals, manipulates the frequency of the output voltage.
The Frequency of the output voltage is what ultimately controls the speed of the motor. By having the capability to change the frequency, the VFD is able to manipulate the speed at which the motor spins.
The benefit of being able to control the speed of the motor, and in turn, the speed of the equipment in your process, is huge. With more precise control of your operation, you can refine the results of your process and dramatically improve your outcome.
Additionally, VFD’s can reduce energy bills. The ability to change the speed of the motor allows processes to run at precisely the right speed.
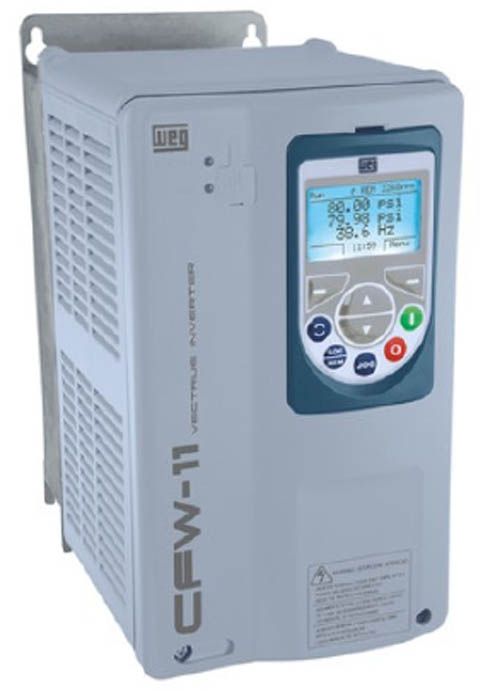
However, there are drawbacks. VFD’s are the highest price of the three motor control options listed in this article. They also produce excess heat due to the IGBT Inverter’s continuous switching. Also, it takes technical knowledge to program them properly and they also have a bigger physical footprint than a motor starter.
There are pros and cons to all three devices mentioned above and the correct choice depends on your specific facility and process. At least now you know the basic difference between the three standard industrial motor control options.
Crossroad Energy Solutions provides services to support your industrial facility’s control system. We have a control panel fabrication facility that builds and certifies general-purpose and hazardous-rated control panels.
Additionally, our field technicians specialize in Electrical, Instrumentation, and Automation maintenance and construction.
Please contact us for more information
1-877-872-0222
info@crossroadenergy.com
