
Electrical Maintenance – Industrial Heaters
November 15, 2021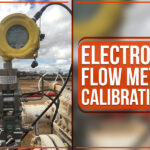
Electronic Flow Meter Calibrations
December 1, 2021Regular electrical equipment maintenance will significantly extend the useful life of your electrical equipment. We’ve covered heaters and I/R scanning already in our November Maintenance Month blog posts, but there are a few stragglers that we’ve missed.
Please remember that there is a severe risk of electrical shock and mechanical danger in performing the tasks listed below when working with electrical equipment. If you are not qualified to take on these tasks, do NOT attempt them.
Ground Impedance
A routine ground impedance test should be performed to ensure that your grounding system is working the way the original installers intended. The most common reason for bad grounding is poor installation.
Faulty grounding can lead to a wide array of safety and equipment problems, including:
- Severe injury or death
- Loss of equipment
- Voltage surges
- Loss of data
- Seemingly random failures that are difficult to identify
- Static build-up and interference
In a perfect world, ground should register zero ohms. There are various ways to check for ground resistance, and your electrician should know which test to use for your specific facility or piece of equipment.
Greasing Electric Motors
This is a critical part of your electric motor maintenance. Electric motors have two main bearings that require lubrication, one on the drive-end and one on the opposite drive-end. Regularly greasing these bearings following the manufacturer’s specifications will ensure that the maximum life of the motor is achieved.
Ensure that you’re using the correct grease, clean off the grease relief plug, apply grease slowly, use the right amount, and be sure to put the grease relief plug back on before finishing.
Busbar Torque
Busbar is a permanent and efficient way to distribute electricity in your electrical equipment, specifically switchgear. Typically, these are made up of metallic strips of copper, brass, or aluminum connected by bolting pieces together.
Manufacturers of electrical equipment will usually have torque ratings for the bolts to hold the bussing together. The bolts need to be periodically checked to ensure that they are tight but not overtightened. Loose connections will eventually cause excess heat, which may lead to electrical fires.
Have your electricians de-energize the busbar and perform the proper lock-out procedures to ensure it is safe to work on it. They can then check the connections for appropriate tightness with a torque wrench and assess if there is any sign of excess heat or corrosion on the bussing. After torquing to the correct rating, apply some torque seal so that it is evident to the next person that these connections were torqued to the manufacture’s specifications.
Proper torquing of bolts on all your electrical equipment is essential and is not limited to the busbar. Breakers, mechanical lugs, grounding, and many other electrical devices have torque ratings listed in the manufacturer’s specifications.
Crossroad Energy Solutions performs routine maintenance for many customers in a variety of industries. We can help you plan and execute your regular maintenance program to extend the life of your equipment.
Crossroad Energy Solutions 1-877-822-0222