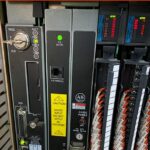
Obsolete PLC5 + SLC500 Migrations
July 12, 2021What is a PLC? What is a DCS? What is an RTU?
The automation world is full of acronyms. RTU, PLC, DCS—but what do these acronyms mean? At Crossroad Energy Solutions, we’ll not only help you understand these acronyms, but we offer support for all these technologies in your area, including in Dallas, Texas. We understand when and where they should be used.
What is a DCS?
A Distributed Control System (DCS) is a central control system for a process. A DCS consists of a Human Machine Interface (HMI) and controllers connected to Input/Output (IO) cards. The HMI can range from a single computer with a single screen to multiple computers each with a quad screen. Typically, a DCS is installed on a large system ranging from 1,000 to 150,000+ IO. DCS systems are designed to concentrate data from multiple sources to give the operator all the information they require to control the process. Facilities using DCS usually require a high degree of uptime and availability, resulting in many redundancies that reduce risk of having a single point of failure. Safety systems (SIS) can further enhance the DCS system’s availability by having a separate system to perform the safety shutdown functions, which leaves the Process Control System (PCS) to focus on the control.
Some examples of industries that use DCS systems are:
- Chemical Plants
- Nuclear Power Plants
- Water/Waste Water Treatment Plants
- Petrochemical Plants
- Refineries
- Oil & Gas Production Facilities
- Manufacturing facilities
DCS systems have a control room or multiple control rooms with multiple servers to connect to the field interfaces. The different DCS vendors have proprietary controllers with communication cards that talk with various fieldbus technologies. This allows them to integrate almost any device into their system. Whether the signal comes from a PLC, an RTU or a transmitter, the DCS can read it. DCS systems have evolved to perform advanced process control algorithms, allowing machine learning to optimize the process.
However, this robust functionality comes at a cost as DCS systems are typically the most expensive control systems.
When trying to decide if a DCS system is the right fit for your process, it is important to ask a few questions:
- What are the redundancy requirements?
- What is the system uptime required?
- What are my interfaces?
There is a large overlap between a small DCS system and a large PLC system. As technology and processing capabilities advance, the line between DCS systems and PLC systems blur. The cost of DCS systems is continuously dropping and the functionality of PLCs is continuously increasing.
What is a PLC?
Programmable Logic Controllers (PLC) are compact computers designed to control a local system. A PLC system typically interfaces to a SCADA or DCS system but can also have a local HMI. PLCs are usually installed on systems less than 1,000 IO. PLCs can come equipped on “pre-packaged equipment,” which are networked together to create a control system. PLCs can be configured with redundancy and perform safety functions, but this would be an added functionality and typically not part of the base product.
PLC systems are found across all industries. Whether they are part of a package in a large facility or controlling a stand-alone piece of equipment, their functionality is powerful and flexible, which makes their presence ubiquitous in all process-driven industries.
PLC systems use a proprietary controller with communication cards to talk to various fieldbus technologies. Unlike DCS systems, these communication interfaces are typically provided by a third-party card or gateway. They also have a wide variety of IO cards to connect whatever type of signal to their system. The processing power is less than a DCS, so it is limited to standard control blocks and will typically only support some of the typical programming languages.
From a cost perspective, PLC systems range greatly but typically fall between DCS systems and RTUs. However, if you want a fully redundant PLC system using multiple controllers and communication interfaces, your costs can surpass a DCS system, but the increased flexibility may make sense in your situation.
What is an RTU?
A Remote Terminal Unit (RTU) is a microcontroller-based device that monitors or controls a field device. RTUs have a larger temperature operating range than a PLC or DCS giving them the ability to operate in remote and harsh environments. RTUs also have a low power usage, allowing them to run off a battery or solar system and communicate (via radio) with the main system. RTUs are usually installed on a small system with less than 100 IO.
RTUs are found in many industries and applications including:
- Oil & Gas Wellsites
- Water and Wastewater Treatment
- Pipelines
- Oil & Gas Flow Measurement
- Tunnels
- Storm Water Monitoring
RTUs are standalone data acquisition and control units. They often come pre-packaged in a junction box for ready for field installation. They have a communication port with the standard communication protocols and a variety of IO channels to connect the standard signals to the system. The processing power of an RTU is limited to basic control functions in standard programming languages
RTUs are the most cost-effective control solution but offer much less functionality compared to a PLC. If you are looking to simply monitor equipment or do some minor control, an RTU might be the right solution for you.
Crossroad Energy Solutions
Advancing technologies continue to level the playing field and the right solution for you can be hard to find. It is important to work with a company that not only understands these ever-changing trends but has an experienced team at its back with a proven track record.
At Crossroad Energy Solutions, we pride ourselves on being “control experts” and offering the right solution for your facility. We provide electrical, instrumentation, and automation services to the oil, gas, and industrial sectors across North America. We are a people-focused company that encourages the personal and professional growth of all our employees.
Let’s work together. Contact us to start talking about the right solution for you.